Background on Al Furat as Envisioned by Iraq in the 1980s
By late 1988, Iraq was in possession of detailed designs of many centrifuge parts, a guide to key suppliers, on-going technical assistance, and aid with its foreign procurement efforts. An immediate outcome of the assistance provided by the H+H team was that Iraq decided to implement quickly the Al Furat project, also called project 112, to create an industrial infrastructure to make thousands of Zippe-type centrifuges.
Iraq recognized that it was unable to make these centrifuges without extensive foreign assistance and procurement. The Iraqi centrifuge experts had matured through their own centrifuge efforts. One of the lessons was to understand their own limitations in making high-precision centrifuge components. Local manufacturing of centrifuge parts for the Beams-type centrifuge during 1987-88 demonstrated the problem of obtaining the accuracy and tolerances for each component. The reasons included poor quality machine tools, inadequate quality control, and a lack of experience in high-precision manufacturing.
However, Iraq's decision to procure the machines needed to make the new, Zippe-type machine was controversial and debated extensively. At the time, Iraq was far from having a tested centrifuge prototype. Should they seek only to acquire important components for a prototype, or should they simultaneously procure manufacturing equipment and raw materials? There were risks with either approach. If the design changed significantly, Iraq could waste both time and money procuring items that would not be necessary in the end. But delay in procuring manufacturing equipment could give Western intelligence agencies more time to learn about Iraq's secret effort and take steps to complicate foreign procurement.
At a key meeting in late 1988, the Iraqi centrifuge officials decided on a plan of action. After balancing options, Iraqi centrifuge officials decided to procure manufacturing equipment and materials before a prototype was developed.
Al Furat Project The goal of this project was to establish a modern facility able to make initially 1,000 centrifuges a year and later 4,000 centrifuges a year. Iraqi planners wanted such a high throughput to account for an anticipated high reject rate in centrifuge components. Given the initial Iraqi Zippe-type centrifuge designs, 1,500 centrifuges operating together in a cascade could produce about 15 kilograms of weapon-grade uranium a year, or enough for one nuclear weapon per year.
From the end of 1988 through mid-1989, Iraq signed most of the important contracts for the Al Furat project. Because the project was based on manufacturing maraging steel rotors, Iraq ordered flow-forming equipment, heat treatment furnaces, materials, specialized welding equipment, and high accuracy computer-numerically-controlled (CNC) machines.
A modern centrifuge plant also requires a specialized working environment with controlled temperature and cleanliness. Al Fao Establishment was made responsible for the engineering design and construction activities at the site, which was at Yousifiya, south of Baghdad. The site had been a mechanical training center, and already had many buildings and utilities that could be adapted relatively easily to the centrifuge plant.
However, Al Fao had no experience in "clean-room" technology or construction. As a result, it contracted with the British company ITSC and the German firm Interatom to build two clean room buildings. Both contracts were signed in the fall of 1989.
In November 1989, Iraq contracted with Interatom to construct building B01, also called central workshop T1250. Iraq knew that Interatom had built clean rooms for centrifuge manufacturing plants and was easy to approach through its office in Baghdad. The value of the contract was about 25 million DM. Iraq did not tell Interatom the true purpose of the building; it declared this building as a tube manufacturing workshop. In reality, B01 would have been dedicated to piping for centrifuge cascades, mechanical testing of single centrifuges, and balancing and final assembly of centrifuges. It was also designed to hold a test cascade of centrifuges. The contract envisioned that construction would be finished in October 1990, although this date would not have been met.
The design of building B01 took months to accomplish, which helps explain the delay in both signing and fulfilling the contract with Interatom. Iraq needed to design the rooms in the building for a purpose that was not stated to Interatom. In this difficult effort, Iraq needed to take special precautions, such as isolating its centrifuge people so that Interatom would not inadvertently learn the true purpose of the building.
In addition, Iraq was constantly learning more about centrifuge manufacturing, requiring changes in the building designs or the specific purpose of rooms. For example, in early 1990 Iraq decided to install a larger cascade of centrifuges in the building. Instead of 36 centrifuges, it decided that it wanted to install a test cascade of 120 centrifuges, able to make one kilogram of 93 percent enriched uranium each year. This change required that the room had to be enlarged and other rooms reduced in size. In the process, the designers had to ensure that other rooms were not reduced to the point that they could not hold the necessary equipment. In another case, Interatom recommended pouring a concrete floor for the entire B01 site to a depth of 80 centimeters. The Iraqis concluded, after lengthy discussions that this procedure would not work in the cascade room, and told Interatom that the floor in this particular room should not be poured uniformly. In the end, the floor is poured concrete but with pits for centrifuge mounts.
Al Fao contracted with the British firm ITSC to design, supply, and erect the utilities and mechanical equipment for building B02. It in turn subcontracted another firm to provide the clean room technology and items. The total contract had a value of about 10 million British pounds. This building was planned to house rotor manufacturing and assembly, bearing assembly, and chemical cleaning and treatment of surfaces. The contract called for construction to be finished by December 1990, but construction was behind schedule.
The other main building was B00, which was a modified building that was part of the original facility. It was intended to hold machines to make specific centrifuge components and manufacture the motors.
Click on any of the images below to see a larger image open in a new window. |
 |
 |
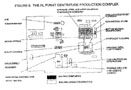 |